Meaningful discussion outside of the potato gun realm. Projects, theories, current events. Non-productive discussion will be locked.
-
wyz2285
- First Sergeant 2
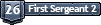

- Posts: 2388
- Joined: Sat Mar 06, 2010 7:50 am
- Location: Porto, Portugal
- Has thanked: 1 time
- Been thanked: 4 times
-
Contact:
Sun May 18, 2014 3:38 pm
I have a 6mm brass tube, 5mm ID. I use it as a low pressure air line and it needs to be bent in several places so I thought about cut it to pieces and solder/blaze them to the shape I want. I tried use tin solder and a mini pen size torch and the solder just doesn't stick. So I bought a bigger torch(one of these with a bottle of gas connected to it) and blazing rod. I heated the tubes until they are red and tired to get the blazing rod to melt and stick to them but it doesn't stick neither.
I ended up heating the tube to red and bend it, got most of the problem solved

but there is still one sharp bend that can only be solved by combine two piece of tube together. What I'm I doing wrong?
CpTn_lAw wrote:

"yay, me wanna make big multishot pnoob with 1000 psi foot pump compressor using diamond as main material. Do you think wet bread make good sealant? "
-
jrrdw
- Moderator
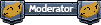

- Posts: 6572
- Joined: Wed Nov 16, 2005 5:11 pm
- Location: Maryland
- Has thanked: 39 times
- Been thanked: 22 times
-
Contact:
Sun May 18, 2014 5:06 pm
Fill the tubing with sand and you should be able to bend it as far as you want with no kinking. Do some testing if you have extra...
-
wyz2285
- First Sergeant 2
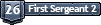

- Posts: 2388
- Joined: Sat Mar 06, 2010 7:50 am
- Location: Porto, Portugal
- Has thanked: 1 time
- Been thanked: 4 times
-
Contact:
Sun May 18, 2014 5:10 pm
Good idea! I thought about filling it with something but never occurred me to use sand. Thanks I'm going to the beach tomorrow and bring a bucket of it

Good ol' Spudfiles, always has answers for everything

CpTn_lAw wrote:

"yay, me wanna make big multishot pnoob with 1000 psi foot pump compressor using diamond as main material. Do you think wet bread make good sealant? "
-
bravootome
- Specialist 3
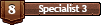

- Posts: 334
- Joined: Mon Oct 14, 2013 11:11 am
- Has thanked: 1 time
- Been thanked: 2 times
Mon May 19, 2014 12:24 am
wyz2285 wrote:Good idea! I thought about filling it with something but never occurred me to use sand. Thanks I'm going to the beach tomorrow and bring a bucket of it

Good ol' Spudfiles, always has answers for everything

i got a tool to bend pipes...cold bending.
come undone
-
wyz2285
- First Sergeant 2
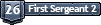

- Posts: 2388
- Joined: Sat Mar 06, 2010 7:50 am
- Location: Porto, Portugal
- Has thanked: 1 time
- Been thanked: 4 times
-
Contact:
Mon May 19, 2014 4:30 am
Are the results any good?
CpTn_lAw wrote:

"yay, me wanna make big multishot pnoob with 1000 psi foot pump compressor using diamond as main material. Do you think wet bread make good sealant? "
-
cammyd32
- Specialist 3
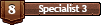

- Posts: 326
- Joined: Fri Apr 29, 2011 7:00 am
Mon May 19, 2014 10:27 am
wyz2285 wrote:I have a 6mm brass tube, 5mm ID. I use it as a low pressure air line and it needs to be bent in several places so I thought about cut it to pieces and solder/blaze them to the shape I want. I tried use tin solder and a mini pen size torch and the solder just doesn't stick. So I bought a bigger torch(one of these with a bottle of gas connected to it) and blazing rod. I heated the tubes until they are red and tired to get the blazing rod to melt and stick to them but it doesn't stick neither.
I ended up heating the tube to red and bend it, got most of the problem solved

but there is still one sharp bend that can only be solved by combine two piece of tube together. What I'm I doing wrong?
Most model engineering grade Brass tubes I have ever come across are often sold with a small amount of surface lacquer or a thin coating of oil to keep a nice finish, before you go at it with anything its always a good idea to sand back the surface just to make sure you are getting to the bare metal.
Apart from that make sure you are using a flux appropriate for either your solder or brazing rod, as without it you would be surprised about how quickly oxidization can occur, and when that happens pretty much nothing will stick, however hot you get it.
-
wyz2285
- First Sergeant 2
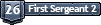

- Posts: 2388
- Joined: Sat Mar 06, 2010 7:50 am
- Location: Porto, Portugal
- Has thanked: 1 time
- Been thanked: 4 times
-
Contact:
Mon May 19, 2014 11:10 am
I sand it, need to try a different flux though, I used one for soldering but didn't help.
CpTn_lAw wrote:

"yay, me wanna make big multishot pnoob with 1000 psi foot pump compressor using diamond as main material. Do you think wet bread make good sealant? "
-
Fnord
- First Sergeant 2
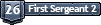
- Posts: 2239
- Joined: Tue Feb 13, 2007 9:20 pm
- Location: Pripyat
- Been thanked: 1 time
-
Contact:
Mon May 19, 2014 12:06 pm
Do you know what actual melting point of your solder/braze is? If it's too close to the tubing's melting point it gets kinda tricky.
Borax should be ok as a flux, if you can't find it try vinegar or diluted drain cleaner.
Normal mid-temp silver solder might be more workable. Alternatively, fill the tubing with lead and bend it however tight you need. Melt the lead back out, heating the ends first and pointing them away from you to avoid getting metal blasted into your face in the event you have a gas bubble trapped inside.
Eye protection is required obviously.
-
wyz2285
- First Sergeant 2
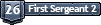

- Posts: 2388
- Joined: Sat Mar 06, 2010 7:50 am
- Location: Porto, Portugal
- Has thanked: 1 time
- Been thanked: 4 times
-
Contact:
Mon May 19, 2014 3:05 pm
No idea, I just grabbed a package of it as I see blazing rod written on it and brass/copper is on of it's applications and it was right next to the torch so I thought it would do, Wouldn't vinegar evaporate??
CpTn_lAw wrote:

"yay, me wanna make big multishot pnoob with 1000 psi foot pump compressor using diamond as main material. Do you think wet bread make good sealant? "
-
Fnord
- First Sergeant 2
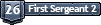
- Posts: 2239
- Joined: Tue Feb 13, 2007 9:20 pm
- Location: Pripyat
- Been thanked: 1 time
-
Contact:
Thu May 22, 2014 8:10 am
Vinegar is difficult to use on anything high temperature, though possible. You have to apply it when it's cooler and work fast before the oxide layer can build up again. A respirator/glasses are required if you use drain cleaner for anything.
Borax is usually ideal, I believe you can find it sold as insect bait/poison in most hardware stores. It tends to flake and pop when it cools down so watch your eyes.
-
Technician1002
- Captain
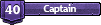
- Posts: 5189
- Joined: Sat Apr 04, 2009 11:10 am
Thu May 22, 2014 11:09 am
Sorry for the late reply, but I've been out a few days. Brass and a brazing rod melt at the same temp if they are the same composition. Joining metals with more of the same metal is called welding. Using a lower temperature metal to join two similar or different metals is called soldering at lower temperatures and brazing at higher temperatures.
Air fuel is almost never used for brazing or welding due to the amount of oxygen in the flame causing the surface to rapidly oxodize. Heating a copper penny (not zinc) or copper wire with a propane torch will show the oxidization clearly.
For "silver Soldering" or brazing with hard silver solder a welding torch is used. The torch is adjusted to a neutral flame (hottest with a clearly defined cone) and then the Oxygen is reduced to create a large feather in the envelope, This is then used to braze or silver solder. The mix in the torch causes all the oxygen to be used in the cone resulting in the feather being completly oxygen free. If you heat copper pipe or a penny in the flame, it will self flux removing the oxide from tarnished pipe making it shiny in the flame. When that happens, the silver solder can be easly added to the pipe and it will flow like water wetting it and flowing into a joint. This is routinely done for refrigeration heat pumps, etc.
Removing the torch when soldering is done will result in instant return of the surface oxide as the hot metal is exposed to air. I hope this helps.
A fluxed brazing rod is best used with a welding torch as an air mix torch is often not hot enough and rapidly burns the flux rendering it ineffective. Brass and steel do not self flux like copper so the flux is used to remove the oxide for brazing.
-
wyz2285
- First Sergeant 2
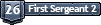

- Posts: 2388
- Joined: Sat Mar 06, 2010 7:50 am
- Location: Porto, Portugal
- Has thanked: 1 time
- Been thanked: 4 times
-
Contact:
Thu May 22, 2014 1:43 pm
Thanks Tech! Now I understand why it wasn't stick! A torch like that cost more than 100 bucks... Would solder it with soldering iron and tin be strong enough? I'd just heat it and bend I guess...
CpTn_lAw wrote:

"yay, me wanna make big multishot pnoob with 1000 psi foot pump compressor using diamond as main material. Do you think wet bread make good sealant? "