Stage1 - 120X CLGG
- jackssmirkingrevenge
- Five Star General
- Posts: 26216
- Joined: Thu Mar 15, 2007 11:28 pm
- Has thanked: 576 times
- Been thanked: 347 times
0_o
Fantastic work. Simple concept, amped up parameters - and 14.4g is nothing for a 0.76" bore!
Fantastic work. Simple concept, amped up parameters - and 14.4g is nothing for a 0.76" bore!
So this would accelerate the piston that compresses the gas for the second stage?the first stage of my upcoming 2-stage light gas gun design
hectmarr wrote:You have to make many weapons, because this field is long and short life
Well, it's about the largest mass that this gun can get up to decent velocity. Projectiles between 5g and 10g will be more common when it's operating as a single stage gun. Pistons for the LGG would be heavier though, between 20g and 60g depending on the other parameters of the shot....14.4g is nothing for a 0.76" bore!
Yes. I still need to do some work on it before that's possible - there seems to be some trouble with the joint between the barrel and the fitting that adapts it to the breech, which leaked when I tried to pull a vacuum on it. I'm planning on hunting that down in a few weeks when I'm home, and in general touching up some of the sketchier parts of the apparatus. I don't actually need the barrel to have a perfect vacuum seal though - I can actively pump it down during a regular shot (with a flow restriction to prevent damage to the vacuum pump), and it only needs to hold off up to 800kPa internal pressure in LGG operation. The chamber also rapidly repressurized right back up to atmospheric after being evacuated, and it would only lose about 1psi/minute when filled to 1700psi with hydrogen. I'm not really sure right now what the source of this discrepancy is, and I didn't have time to properly evaluate it at the end of the summer.So this would accelerate the piston that compresses the gas for the second stage?
Spudfiles' resident expert on all things that sail through the air at improbable speeds, trailing an incandescent wake of ionized air, dissociated polymers and metal oxides.
- jackssmirkingrevenge
- Five Star General
- Posts: 26216
- Joined: Thu Mar 15, 2007 11:28 pm
- Has thanked: 576 times
- Been thanked: 347 times
It it desirable to have a heavy piston in this case, to maintain the compression momentum so to speak? Have you modelled how piston weight would affect performance?DYI wrote:Pistons for the LGG would be heavier though, between 20g and 60g depending on the other parameters of the shot.
hectmarr wrote:You have to make many weapons, because this field is long and short life
Generally speaking, piston weight should be chosen based on the desired pressure profile - a heavier piston will travel slower and tend to reduce the amount by which the pressure spikes above the disk rupture pressure. Varying piston mass makes possible a great deal of tuning, for example to try to maintain a constant base pressure on the projectile.
I have modelled this pretty extensively using the GALE code. I think I actually included how to model multi-stage launchers in the user's guide I sent you.
I have modelled this pretty extensively using the GALE code. I think I actually included how to model multi-stage launchers in the user's guide I sent you.
Spudfiles' resident expert on all things that sail through the air at improbable speeds, trailing an incandescent wake of ionized air, dissociated polymers and metal oxides.
I just finished drawing the second stage, and am hoping for some feedback before I start building it. This drawing shows only the second stage components and some selected dimensions. The pump tube will thread into the 1"-32 threaded port at the left of the image, and the barrel continues on well past the right side. The configuration here is for a shear skirt or detaching-disc projectile. When using a petalling disc, there would be a relief cut into the breech to accommodate the petals, to avoid restricting the flow. Also note the small seal on the connection between the end of the pump tube and the start of the cone - it will be cut with a face grooving tool and filled with a tight fitting brass or plastic ring.
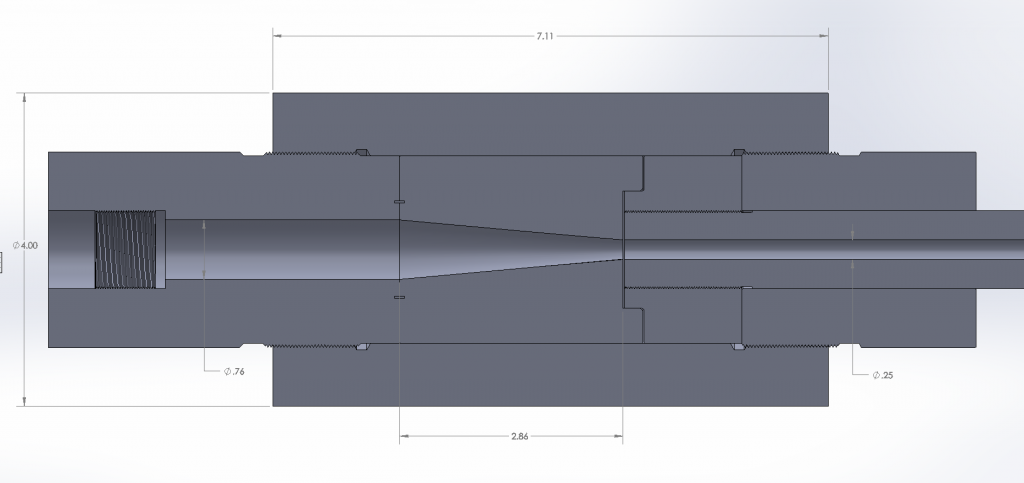
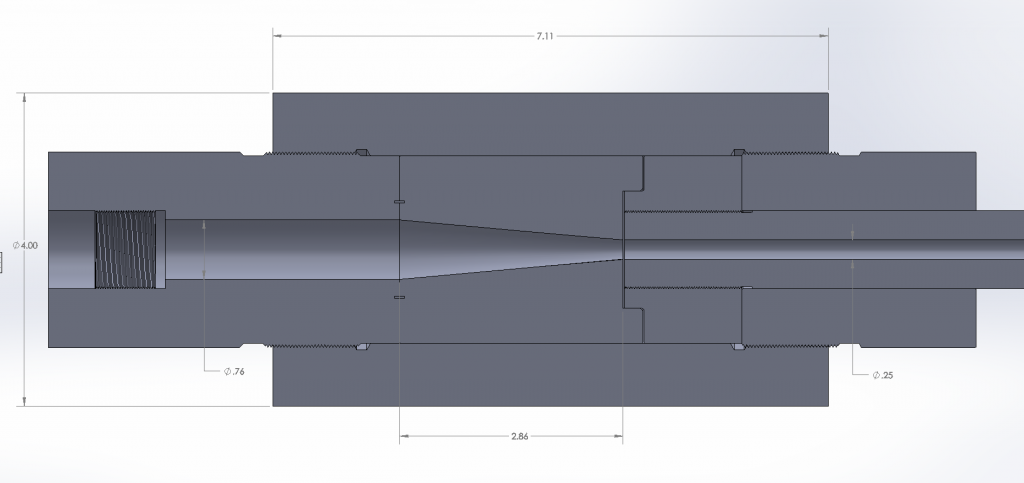
Spudfiles' resident expert on all things that sail through the air at improbable speeds, trailing an incandescent wake of ionized air, dissociated polymers and metal oxides.
- bravootome
- Specialist 3
- Posts: 334
- Joined: Mon Oct 14, 2013 11:11 am
- Has thanked: 1 time
- Been thanked: 2 times
i was just going to ask what can i use to overpass the 500-600 psi pressure i use to my guns. I was thinking about 80 bar...
I read somewhere that if i connect 2 fridge compressors (output of first to input of second) i may go @70 bar even 80 bar...(i did recycled 4 of them
)
So, i know it will work, but isn't the second comp, going to broke at a moment, sooner, ?
i must say i got a 5th comp. from a Water cooling XXX( that machine used for cooling and heating water...) witch is much much smaller than a normal fridge comp. ( so better for used as second comp. in my system )
What should i do, make a pump or go with compressors ?
I read somewhere that if i connect 2 fridge compressors (output of first to input of second) i may go @70 bar even 80 bar...(i did recycled 4 of them

So, i know it will work, but isn't the second comp, going to broke at a moment, sooner, ?
i must say i got a 5th comp. from a Water cooling XXX( that machine used for cooling and heating water...) witch is much much smaller than a normal fridge comp. ( so better for used as second comp. in my system )
What should i do, make a pump or go with compressors ?
come undone
I now have a reliable parting tool and a bandsaw, making it much easier to produce burst disks and integral shear skirt projectiles for this launcher.
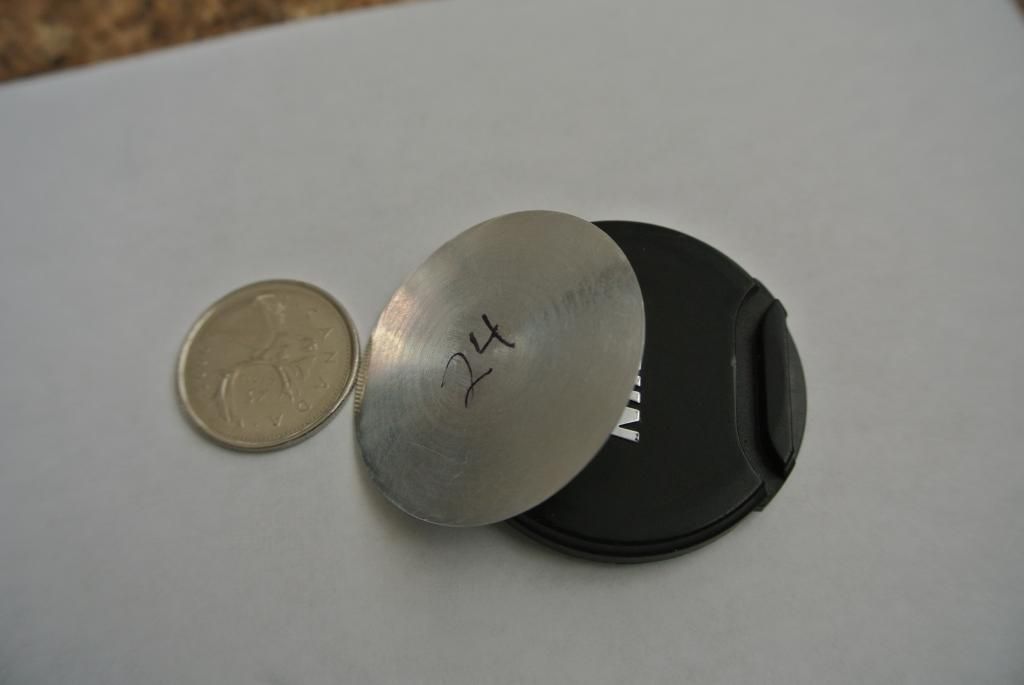
This is an example, 0.024" thick, made of 7068-T6511 aluminum, with a rupture pressure of about 6700psi. The surface finish on the parted side is smooth to the touch. I can make one of these in less than 20 minutes. I'm hoping to get ten or more shots over the winter break, barring any unfixable problems. Some of these will be done for diagnostic purposes, but there should be time for several "fun" shots in there. Any suggestions on target/projectile combinations?
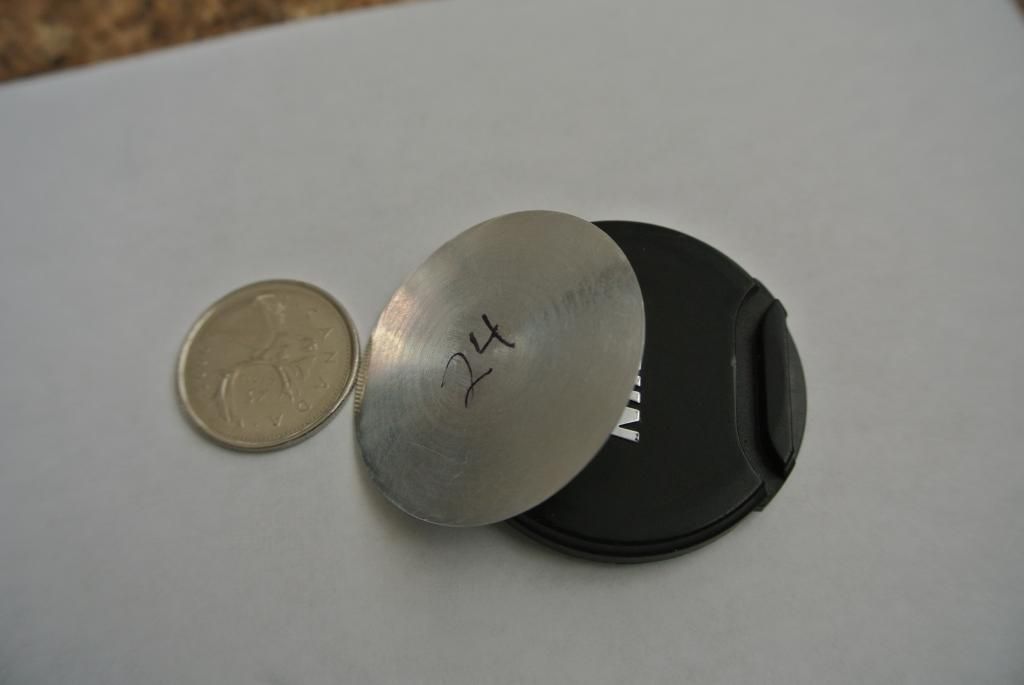
This is an example, 0.024" thick, made of 7068-T6511 aluminum, with a rupture pressure of about 6700psi. The surface finish on the parted side is smooth to the touch. I can make one of these in less than 20 minutes. I'm hoping to get ten or more shots over the winter break, barring any unfixable problems. Some of these will be done for diagnostic purposes, but there should be time for several "fun" shots in there. Any suggestions on target/projectile combinations?
Spudfiles' resident expert on all things that sail through the air at improbable speeds, trailing an incandescent wake of ionized air, dissociated polymers and metal oxides.
- jackssmirkingrevenge
- Five Star General
- Posts: 26216
- Joined: Thu Mar 15, 2007 11:28 pm
- Has thanked: 576 times
- Been thanked: 347 times
Cliche perhaps but spaced steel plates/tungsten cored darts?DYI wrote:Any suggestions on target/projectile combinations?

What velocities are you predicting?
Will it look anything like this on a smaller scale?
[youtube][/youtube]
hectmarr wrote:You have to make many weapons, because this field is long and short life
I don't have any tungsten at the moment. It's rather expensive, you know... I do have a few inches of 1/4" tungsten carbide round, and a design for a sabot which should allow launching a 10g chunk of if at ~1100m/s. I also have a sabot catcher (as yet untested). Should be able to launch a 3/8" steel ball at 1500m/s. Apart from that, I have what you'd expect to find in a small shop - various sizes of steel, copper, brass, aluminum, and a few plastics.Cliche perhaps but spaced steel plates/tungsten cored darts?
The table below nicely summarizes the performance envelope. For anything higher than 30g, assume a constant muzzle energy of 9.3kJ. Please excuse the lack of a proper graph.What velocities are you predicting?
30g ---- 790m/s
20g ---- 955m/s
15g ---- 1090m/s
10g ---- 1310m/s
7.5g --- 1485m/s
5g ------ 1760m/s
3.5g ---- 2025m/s
No.Will it look anything like this on a smaller scale?
Spudfiles' resident expert on all things that sail through the air at improbable speeds, trailing an incandescent wake of ionized air, dissociated polymers and metal oxides.
- jackssmirkingrevenge
- Five Star General
- Posts: 26216
- Joined: Thu Mar 15, 2007 11:28 pm
- Has thanked: 576 times
- Been thanked: 347 times
Foley huck.
Would you like me to send you a couple of these? What's the diameter of your firing barrel?
Will you be testing this at point blank range or will there be some distance between muzzle and target?
It's also rather brittle and prone to shattering. I've switched to HSS blanks ground to a point as the basis of my own endeavors.I don't have any tungsten at the moment. It's rather expensive, you know...
Would you like me to send you a couple of these? What's the diameter of your firing barrel?
Will you be testing this at point blank range or will there be some distance between muzzle and target?
hectmarr wrote:You have to make many weapons, because this field is long and short life
Huh? Midwest Tungsten claims elongation at break from 8% to 14% for their range of tungsten alloys, with hardnesses from HRC24 - 28 and yield strengths from 85 - 90ksi. Hardly sounds brittle to me - certainly less so than hardened HSS or or tungsten carbide.It's also rather brittle and prone to shattering.
Based on the typical results of those endeavours, I think you'd be better served by spending less time on the machining and more time on the stress analysisI've switched to HSS blanks ground to a point as the basis of my own endeavors.

The barrel diameter is .760". I can order HSS blank easily enough from my tooling suppler. Unfortunately, I only have square blanks on hand at the moment, but I wouldn't mind converting a drill bit or two if there was a sufficiently enticing idea. I also have a spare centre punch massing about 70g that I might consider launching, and another one of those 3/8" tungsten carbide balls that I launched through a 3/8" plate back in 2013.Would you like me to send you a couple of these? What's the diameter of your firing barrel?
Muzzle to target spacings up to about 5 metres can be accomodated. Just remember, I'm shooting inside, so there are certain limitations on what can be attempted. I can fire anything at anything else inside my containment vessel, but this limits the spacing to one metre.Will you be testing this at point blank range or will there be some distance between muzzle and target?
Spudfiles' resident expert on all things that sail through the air at improbable speeds, trailing an incandescent wake of ionized air, dissociated polymers and metal oxides.
- jackssmirkingrevenge
- Five Star General
- Posts: 26216
- Joined: Thu Mar 15, 2007 11:28 pm
- Has thanked: 576 times
- Been thanked: 347 times
I was referring to tungsten carbide. Having said that the tungsten fishing sinker I had sent to DR had survived the impact with a 1/2" steel plate intact.DYI wrote:Huh? Midwest Tungsten claims elongation at break from 8% to 14% for their range of tungsten alloys, with hardnesses from HRC24 - 28 and yield strengths from 85 - 90ksi. Hardly sounds brittle to me - certainly less so than hardened HSS or or tungsten carbide.
Based on the typical results of those endeavours, I think you'd be better served by spending less time on the machining and more time on the stress analysis



I'm learning, certainly have a lot more appreciation for the forces involved than I did when I first started out.
Is that 0.760" exactly? I have some 7.5mm dia round HSS blanks knocking about, could make a couple of aluminum finned darts if you want. What's the inner diameter of your sabot catcher?The barrel diameter is .760". I can order HSS blank easily enough from my tooling suppler. Unfortunately, I only have square blanks on hand at the moment
hectmarr wrote:You have to make many weapons, because this field is long and short life
That is 0.760"±0.0005". I find that making the projectile body to 0.759" gives a nice smooth slide. I'd probably increase that to .760" for a projectile with a softer body. The part of the sabot catcher that actually stops the sabot takes about 20 minutes to machine. It can be any diameter it needs to be.Is that 0.760" exactly? I have some 7.5mm dia round HSS blanks knocking about, could make a couple of aluminum finned darts if you want. What's the inner diameter of your sabot catcher?
Have you got those finned darts working consistently out of the shotgun yet? I remember very vividly how Larda lost the first HyGaC20 barrel, and I would prefer to avoid a repeat on mine. I spent a few days designing a tungsten carbide core round in ANSYS about two weeks ago, and the stresses involved in supporting a rod like that by the base (rather than threading along the diameter, like most APFSDS rounds do) are severe, even with clever stress spreading and a 7068 aluminum sabot. What alloy are you using for your sabots? 7075?
Spudfiles' resident expert on all things that sail through the air at improbable speeds, trailing an incandescent wake of ionized air, dissociated polymers and metal oxides.
- jackssmirkingrevenge
- Five Star General
- Posts: 26216
- Joined: Thu Mar 15, 2007 11:28 pm
- Has thanked: 576 times
- Been thanked: 347 times
Taofledermaus just received the latest batch with the central finlets at the CG which should prevent the projectile destabilizing in the barrel. I guess I should wait for him to test them before being able to claim consistency, he might do it as soon as next weekend depending on the weather.Have you got those finned darts working consistently out of the shotgun yet? I remember very vividly how Larda lost the first HyGaC20 barrel, and I would prefer to avoid a repeat on mine.
It's effectively the same as the Russian BM15 APFSDS round where the fins ride the bore but instead of a discarding central sabot, the CG is supported by the finlets and the sabot is just a pusher disk. I see what you mean about the stress patterns, the Russian dart is being pulled by the sabot as opposed to being pushed, resulting in a completely different type of environment for the projectile during acceleration. The problem with replicating APFSDS though is having sabot petals which would fit together well enough to form an effective seal, something which would be a pain in the ass to machine.
For this design it would only need a pusher disk so no need to destroy a sabot catcher really.
Your typical general purpose 6061, nothing exceptional.What alloy are you using for your sabots? 7075?
hectmarr wrote:You have to make many weapons, because this field is long and short life