Peak pressure measurement.
- D_Hall
- Staff Sergeant 5
- Posts: 1924
- Joined: Thu Feb 07, 2008 7:37 pm
- Location: SoCal
- Has thanked: 8 times
- Been thanked: 44 times
OK, so in the Pipe Dream thread I mentioned that I've got access to high speed pressure transducers (20 kHz response). They're neato toys, but they're not cheap. Not even by military funding standards.
But peak pressure surely must be a useful piece of information when designing/analyzing our toys! How does one get this information on a budget?
Two thoughts.....
1) An engine compression tester. Only problem I see with this is that the gases captured will be cooling quickly so you've got to get your reading quickly. In fact, it could be that this just isn't practical due to the speed required.
2) If the above won't work, I'm thinking of a similar system but with a cheaper (low frequency response) pressure transducer. Theoretically this is the same system, it's just automating the measurement.
Biggest problem I can see is possible momentum issues with the check value.
Thoughts?
But peak pressure surely must be a useful piece of information when designing/analyzing our toys! How does one get this information on a budget?
Two thoughts.....
1) An engine compression tester. Only problem I see with this is that the gases captured will be cooling quickly so you've got to get your reading quickly. In fact, it could be that this just isn't practical due to the speed required.
2) If the above won't work, I'm thinking of a similar system but with a cheaper (low frequency response) pressure transducer. Theoretically this is the same system, it's just automating the measurement.
Biggest problem I can see is possible momentum issues with the check value.
Thoughts?
- rna_duelers
- Staff Sergeant 3
- Posts: 1739
- Joined: Mon Sep 26, 2005 7:07 am
- Location: G-land Australia
Well the Check Valve peak pressure tester has been used many times with good results but I always questioned the gases cooling and giving a lower reading then the actually achieved highest pressure.
You could give the engine compression tester a go,and if it doesn't work it's only $20.I've always been interested in the use of one of these in testing the peak pressure,let me know how it goes.
You could give the engine compression tester a go,and if it doesn't work it's only $20.I've always been interested in the use of one of these in testing the peak pressure,let me know how it goes.
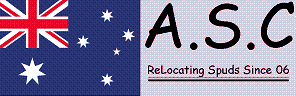
- jimmy101
- Sergeant Major 2
- Posts: 3206
- Joined: Wed Mar 28, 2007 9:48 am
- Location: Greenwood, Indiana
- Has thanked: 6 times
- Been thanked: 18 times
- Contact:

Generic tire pressure pencil gauges are peak pressure recorders. Get a good one, McMaster has them rated up to 160 PSIG (for example part no. 6637A66).
This type of gauge has been proposed as an extremely cheap way of recording explosions in closed mine shafts.
The photo above shows a cheap one. The plastic head that has the fitting for the schrader just pulls off the gauge body.
The only problem I've had with them are;
1. The $2 ones I've been using leak (blowby around the piston) like crazy above about 80 PSIG.
2. The blowby causes the scale to read high since the moving gases actually tend to shove the scale out independent of the position of the internal piston.
3. The moving scale has inertia, given the high rate of pressure rise in a spudgun they tend to read high since the scale overshoots. It should be possible to overcome this by adding more friction to the moving scale.
The cheapo $2 ones fit nicely in a 3/8" (or was it a 1/4"?) compression fitting. (For mine, I needed to hone out the ferrule just a tiny bit.)
Alternative 2, build your own based on the design of the tire pressure pencil gauge.

The Engine Compression Tester is probably your best bet. You can get ones that screw into the spark plug threads and has a peak pressure needle that once it goes up it will not come down until you reset it. So therefore you can screw this thing into your chamber and be set to get multiple shots with it to get all your data for comparing shots.
<a href="">DONT TAZE ME BRO.. DONT TAZE ME... AHHHH</a>Yea, that's definitely going to get you at least a tazer.
facebook.com/biggrib
- jimmy101
- Sergeant Major 2
- Posts: 3206
- Joined: Wed Mar 28, 2007 9:48 am
- Location: Greenwood, Indiana
- Has thanked: 6 times
- Been thanked: 18 times
- Contact:
There are a couple of problems with the cylinder compression testers. The first is that they were designed to give the correct reading after several compression cycles. Essentially, they are "pumped up" to their final reading over several revolutions of the engine.BigGrib wrote:The Engine Compression Tester is probably your best bet. You can get ones that screw into the spark plug threads and has a peak pressure needle that once it goes up it will not come down until you reset it. So therefore you can screw this thing into your chamber and be set to get multiple shots with it to get all your data for comparing shots.
Secondly they are really mass detectors, that is, they detect the greater density of the gases casued by compression. In a combustion gun there is pretty little change in the density of the gases, the increased pressure is due to the much higher temperature. Pumping ~2500C gases into the gauge may be a problem because of heat loss.

it's worth a try none the less and all you're doing is installing a fitting that you can screw the compression tester into and when not in use you can put a plug in it
<a href="">DONT TAZE ME BRO.. DONT TAZE ME... AHHHH</a>Yea, that's definitely going to get you at least a tazer.
facebook.com/biggrib
- jimmy101
- Sergeant Major 2
- Posts: 3206
- Joined: Wed Mar 28, 2007 9:48 am
- Location: Greenwood, Indiana
- Has thanked: 6 times
- Been thanked: 18 times
- Contact:
Yep. If you already have a cylinder compression gauge it would certainly be worth a try.BigGrib wrote:it's worth a try none the less and all you're doing is installing a fitting that you can screw the compression tester into and when not in use you can put a plug in it
Personally though, I don't think I would buy one just to see if it'll work, too expensive.
If someone does have one, I wonder if it does "pump up" after more than one shot?

- Pete Zaria
- Corporal 5
- Posts: 954
- Joined: Fri Mar 31, 2006 6:04 pm
- Location: Near Seattle, WA
I'll admit this is a bit of an out-there idea, but...
What about rigging up a digital camera to take an image of a pressure gauge a few milliseconds after ignition? You could use a relay to fire the camera at the same time the spark system fires.
You'll want to use a high shutter speed such as 1/500th, and you'll need a bright light source illuminating the gauge to get a good picture at this high shutter speed. However, you can probably adjust the shutter speed to allow a bit of "lag" so the camera can "catch" the needle in action. At a lower shutter speed such as 1/60th or so, you'll get a blurry picture of the needle moving, but it should be easy enough to tell where it stopped.
Just a thought. The repeated pressure spikes would probably destroy the gauge.
There are so many factors at play here, getting an accurate reading seems nearly impossible. A truly accurate reading might only be possible with a very well-constructed sealed chamber. I'm not sure.
Peace,
Pete Zaria.
What about rigging up a digital camera to take an image of a pressure gauge a few milliseconds after ignition? You could use a relay to fire the camera at the same time the spark system fires.
You'll want to use a high shutter speed such as 1/500th, and you'll need a bright light source illuminating the gauge to get a good picture at this high shutter speed. However, you can probably adjust the shutter speed to allow a bit of "lag" so the camera can "catch" the needle in action. At a lower shutter speed such as 1/60th or so, you'll get a blurry picture of the needle moving, but it should be easy enough to tell where it stopped.
Just a thought. The repeated pressure spikes would probably destroy the gauge.
There are so many factors at play here, getting an accurate reading seems nearly impossible. A truly accurate reading might only be possible with a very well-constructed sealed chamber. I'm not sure.
Peace,
Pete Zaria.
- VH_man
- Staff Sergeant 4
- Posts: 1827
- Joined: Sat Dec 09, 2006 6:00 pm
- Location: New Hampshire
- Been thanked: 1 time
what about a check-valve and a pressure guage (with a pressure release valve added in...). I used this method to measure pressures in different parts of my pneumatic once....
(it was kinda cool, i had them set up every foot down the barrel)
(it was kinda cool, i had them set up every foot down the barrel)
- Pete Zaria
- Corporal 5
- Posts: 954
- Joined: Fri Mar 31, 2006 6:04 pm
- Location: Near Seattle, WA
It's been tried.VH_man wrote:what about a check-valve and a pressure guage (with a pressure release valve added in...). I used this method to measure pressures in different parts of my pneumatic once....
(it was kinda cool, i had them set up every foot down the barrel)
First of all you have to use a T.
If you imagine the T oriented like a letter T, with the bottom leg leading to the chamber, you need the check valve between the chamber and the T, the pressure gauge on one "side", and a ball valve to release the pressure after the shot on the other "side".
Second, it's not very accurate because A) the area behind the check valve naturally won't see as much pressure as the combustion chamber itself does. B) temperature plays a huge role, and the temperature of the combusting gases goes down very quickly after combustion, so taking an accurate reading would be very difficult.
I've also considered modifying a digital tire gauge which records peak pressure, but it wouldn't last long subjected to such treatment.
Peace,
Pete Zaria.
- D_Hall
- Staff Sergeant 5
- Posts: 1924
- Joined: Thu Feb 07, 2008 7:37 pm
- Location: SoCal
- Has thanked: 8 times
- Been thanked: 44 times
jimmy101 wrote:Personally though, I don't think I would buy one just to see if it'll work, too expensive.

The whole reason I got the idea was I saw one on sale for something like $10.
- D_Hall
- Staff Sergeant 5
- Posts: 1924
- Joined: Thu Feb 07, 2008 7:37 pm
- Location: SoCal
- Has thanked: 8 times
- Been thanked: 44 times
Umm.... You are aware that there are pressure gages that have secondary needles that "save" the max reading, right?Pete Zaria wrote:I'll admit this is a bit of an out-there idea, but...
What about rigging up a digital camera to take an image of a pressure gauge a few milliseconds after ignition? You could use a relay to fire the camera at the same time the spark system fires.
Only issue is that I doubt a traditional pressure gage has the frequency response required.
- D_Hall
- Staff Sergeant 5
- Posts: 1924
- Joined: Thu Feb 07, 2008 7:37 pm
- Location: SoCal
- Has thanked: 8 times
- Been thanked: 44 times
That's what a compression tester is.VH_man wrote:what about a check-valve and a pressure guage (with a pressure release valve added in...). I used this method to measure pressures in different parts of my pneumatic once....
You could always make your own not-so-snazzy pressure transducer.
I don't believe an electromagnetic one would be either too expensive or impractical.
A coil and a magnet basically.
Put some resistance (a spring say) on the magnet and expose it possibly through a piston in a tube to the chamber.
The magnet moves within a coil of wire and when a pressure spike comes along it gets shoved, generating a current in the coil.
Or for a very lightweight moving part you move the coil and have the magnet stationary (as in a speaker/microphone).
The trick would really be to lower the forces enough to connect them to the transducer and then of course to calibrate it
I don't believe an electromagnetic one would be either too expensive or impractical.
A coil and a magnet basically.
Put some resistance (a spring say) on the magnet and expose it possibly through a piston in a tube to the chamber.
The magnet moves within a coil of wire and when a pressure spike comes along it gets shoved, generating a current in the coil.
Or for a very lightweight moving part you move the coil and have the magnet stationary (as in a speaker/microphone).
The trick would really be to lower the forces enough to connect them to the transducer and then of course to calibrate it
