
how safe is soldering copper cannons
solder is not gunna be strong enough to take any pressure, it is used strictly for electrical work and isnt strong at all.
i think for copper u use a tekneek called sweating, its on the wiki
copper can take a fair bit i think.
soz 4 the spelling i cnt b bopthered
i think for copper u use a tekneek called sweating, its on the wiki
copper can take a fair bit i think.
soz 4 the spelling i cnt b bopthered
-
- Private
- Posts: 9
- Joined: Sun Dec 18, 2005 6:17 pm
would using epoxy resin (which ive read on this site can take up to 2000 psi (wtf?)) be ok, as long as the joints are tight and strong?
i wouldnt, some epoxies dont bond well to metal, soldering is easy once you get the hang of it, maneuvering the propane torch is a bit difficult at first, make sure you have some heat resistant gloves (i use welders gloves) as a precaution, i've almost grabbed a hot piece of copper as it was falling, just a reflex.
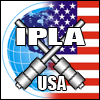
- boilingleadbath
- Staff Sergeant 2
- Posts: 1635
- Joined: Sat Mar 12, 2005 10:35 pm
- Location: Pennsylvania, USA
A search indicates that the shear strength of tin-lead solder is about 5400 PSI. Although we don't know for certain, the shear strength of epoxy may well be less than the tensile strength, which is written on the package.
Thus, assuming that you are using an epoxy which makes good bonds to metals, epoxy should be fine for roughly 1/2 to 1/3 of the rating of a soldered joint. Going on memory, that's about 150-100 PSI... in which case you'd be better off using PVC.
Thus, assuming that you are using an epoxy which makes good bonds to metals, epoxy should be fine for roughly 1/2 to 1/3 of the rating of a soldered joint. Going on memory, that's about 150-100 PSI... in which case you'd be better off using PVC.
soldering the pipes is your best bet. Its not all that hard to do either, i would suggest practicing a few times before you do it to your cannon.
Technically, its almost the same thing as cementing PVC together. You flux the copper pipe before you solder like you use PVC solvent before you use cement. The trick is gettting the solder to "suck in between" the fitting and pipe. a little trick i use is to add a little flux to the hot solder once you think that the weld is complete. The flux adds to the capilary action of the solder, possibly showing you a spot you could have missed.
As a precaution i would pressure test the copper pipe with air before using it for combustion.
Technically, its almost the same thing as cementing PVC together. You flux the copper pipe before you solder like you use PVC solvent before you use cement. The trick is gettting the solder to "suck in between" the fitting and pipe. a little trick i use is to add a little flux to the hot solder once you think that the weld is complete. The flux adds to the capilary action of the solder, possibly showing you a spot you could have missed.
As a precaution i would pressure test the copper pipe with air before using it for combustion.
- boilingleadbath
- Staff Sergeant 2
- Posts: 1635
- Joined: Sat Mar 12, 2005 10:35 pm
- Location: Pennsylvania, USA
Testing it with air wouldn't be any safer than just using it strait up... test it when it's filled with water. That way, if it fails, it'll only go "pop" and spill water every where - instead of going "BANG" and blowing a copper endcap through your window.