Air tank alternative: fiberglass-reinforced soda bottles
Ah, soda bottles. I can't help you fix the flow problems, but I can point out that adapters have been made, though good luck trying to find them now.
The adapters were soda bottle thread on one side, 3/4" female NPT on the other, with a small hole in the side, with 1/4" female NPT threads for a fill valve, guage, or pop-off valve.
<a href="http://thumbs.villagephotos.com/18682253.jpg">Small</a>
<a href="http://thumbs.villagephotos.com/18682261.jpg">Small</a>
<a href="http://img.villagephotos.com/p/2003-9/3 ... .JPG">Soda bottle dart gun</a>
I believe these were injection molded polyurethane, just like the custom valve tops that were made (also seen in that picture). I have a couple valve tops but I've never had one of the bottle adapters, so no first hand experience with them here.
The adapters were soda bottle thread on one side, 3/4" female NPT on the other, with a small hole in the side, with 1/4" female NPT threads for a fill valve, guage, or pop-off valve.
<a href="http://thumbs.villagephotos.com/18682253.jpg">Small</a>
<a href="http://thumbs.villagephotos.com/18682261.jpg">Small</a>
<a href="http://img.villagephotos.com/p/2003-9/3 ... .JPG">Soda bottle dart gun</a>
I believe these were injection molded polyurethane, just like the custom valve tops that were made (also seen in that picture). I have a couple valve tops but I've never had one of the bottle adapters, so no first hand experience with them here.
I do remember watching some of AntiGravity Research's videos, I believe they used carbon fiber instead of fiberglass, but yeah, it's not that new.MRR wrote:Reenforcing water bottles with fibreglass and epoxy is actually not that new. The current world record holder in water bottle launching use up to 1300 psi in their creations.
A lot of people have actually used no-stretch fishing line wrapped around fluorescent tube covers (thin walled polycarbonate tubes for protecting fluorescent lights) and glued on with polyurethane glue to increase the pressure rating for a smaller diameter pressure vessel.
From their videos/photos, AirCommandRockets paints on epoxy and then applies the fiberglass then paints it again, just as JSR said.
For the prototype tank I'm working on I will be using strapping tape, so I don't have to mess with epoxy and such. I used a heat gun to make the base of the bottle more hemispherical, so the tape will go over it better. I'm also going to shrink another bottle on top of the tape to provide further protection.
For the connector I'm thinking of trying a 3/4" compression adapter, since the threaded portion has an OD just a bit larger than 3/4" pipe. If it doesn't seal by itself or with an o-ring or something, I'll have to look for a way to make threaded adapters or something.
I've actually done this before, but I want to try and find a method that doesn't require cutting new threads with an adapter.
- jackssmirkingrevenge
- Five Star General
- Posts: 26216
- Joined: Thu Mar 15, 2007 11:28 pm
- Has thanked: 576 times
- Been thanked: 347 times
There was one meant to fit them as disposable suppressorsnoname wrote:adapters have been made

- Attachments
-
- sodaadapter.jpg (12.34 KiB) Viewed 6184 times
hectmarr wrote:You have to make many weapons, because this field is long and short life
I did come across a few threads asking if using them actually worked. I doubt those would be very air-tight, though, and the thread probably wouldn't be compatible with anything at all. Maybe someone with CNC access can churn a few out and sell them? bottle thread to 3/4" NPT would be nice.jackssmirkingrevenge wrote:There was one meant to fit them as disposable suppressorsnoname wrote:adapters have been made
I still think it would be more useful to come up with something more accessible though.
Here is the tank I finished today, 1L volume. It reminds me of composite/carbon fiber paintball tanks because of the fibers showing through the outer plastic layers.
First to clean and prep the bottle: remove label and shape bottom
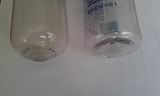
Then begin applying tape:
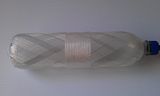
After tape is all applied, add more bottles for protection: right side is bottom bottle and right side is top bottle
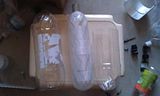
Final Product
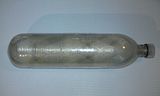
I went a bit overboard and used some fairly thick 1.5L bottles to do the outer covering. I had to use a lot of heat to get the bottles to shrink correctly and I melted some of the tape underneath. But the thickness of the two bottles makes up for it. When I make my next one I'll use thin walled water bottles to reduce the weight and prevent overheating.
I donned some safety glasses and tested it: Pressurized to 80PSI, I put it on some concrete and hit it with a metal pole from a few feet away. No noticeable damage. I have yet to do a high pressure test (the highest I can go is 150PSI) but I don't think this tank will be breaking anytime soon.
The next step is to figure out a connection system.
First to clean and prep the bottle: remove label and shape bottom
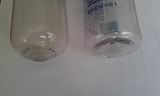
Then begin applying tape:
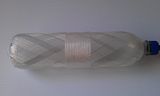
After tape is all applied, add more bottles for protection: right side is bottom bottle and right side is top bottle
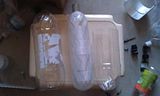
Final Product
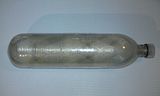
I went a bit overboard and used some fairly thick 1.5L bottles to do the outer covering. I had to use a lot of heat to get the bottles to shrink correctly and I melted some of the tape underneath. But the thickness of the two bottles makes up for it. When I make my next one I'll use thin walled water bottles to reduce the weight and prevent overheating.
I donned some safety glasses and tested it: Pressurized to 80PSI, I put it on some concrete and hit it with a metal pole from a few feet away. No noticeable damage. I have yet to do a high pressure test (the highest I can go is 150PSI) but I don't think this tank will be breaking anytime soon.
The next step is to figure out a connection system.
- jackssmirkingrevenge
- Five Star General
- Posts: 26216
- Joined: Thu Mar 15, 2007 11:28 pm
- Has thanked: 576 times
- Been thanked: 347 times
I used to work in the industry and part of the routine testing was to hydrotest a bottle from each mould to burst pressure. Half litre bottles of iced tea would fail at around 300-310 psi, and right before they would balloon dramatically.
hectmarr wrote:You have to make many weapons, because this field is long and short life
80 PSI was a preliminary test with my bike pump, as I couldn't test with my air compressor at 150PSI. I was also testing impact resistance, something I would not want to try with a PVC tank.wyz2285 wrote:A normal coke bottle takes 80 psi without problem too![]()
Don´t know why you need to do this
If a coke bottle is rated for 150 PSI and you use it at 120PSI, you have a safety factor of 1.25, but things like scratches, folds, and dents can decrease the safe maximum pressure, increasing the risk of a failure.
If you reinforce a coke bottle to withstand 300PSI and you use it at 150PSI, you have a safety factor of 2 and the added benefit of protection from scratches and other damages, making a tank like this last much longer and reducing risk.
I'm just putting this info here for people who want to use it. If you're fine with a regular soda bottle as an air tank, I'm not stopping you.
I have some .5 liter bottles that held sparkling lipton iced tea. The plastic was much thicker than normal .5 liter bottles, so they withstand much higher pressures. I suspect they use the same form for two different sizes of bottles, so when they blow-mold the smaller bottle, it doesn't expand as much and leaves thicker walls.jackssmirkingrevenge wrote:I used to work in the industry and part of the routine testing was to hydrotest a bottle from each mould to burst pressure. Half litre bottles of iced tea would fail at around 300-310 psi, and right before they would balloon dramatically.
- jackssmirkingrevenge
- Five Star General
- Posts: 26216
- Joined: Thu Mar 15, 2007 11:28 pm
- Has thanked: 576 times
- Been thanked: 347 times
In general, PET bottles are made to the absolute minimum specifications. The preforms that become the bottles are sold by weight, this translates into smaller material, transport and waste disposal costs if the same bottle can be made with a lighter preform.aEx155 wrote:I have some .5 liter bottles that held sparkling lipton iced tea. The plastic was much thicker than normal .5 liter bottles, so they withstand much higher pressures. I suspect they use the same form for two different sizes of bottles, so when they blow-mold the smaller bottle, it doesn't expand as much and leaves thicker walls.
Water bottles are the worst, they only need to resist the weight of other bottles stacked on top of them. Those made for carbonated drinks are more resistant, but many times it's a matter of luck how much a particular bottle can take. The blowmoulding process is very sensitive to temperature and pressure variables, I could easily take two bottles from the same mould made within minutes of eachother, and one will hold to 350 psi without bursting, the other will fail at 200.
hectmarr wrote:You have to make many weapons, because this field is long and short life
- Major Collins
- Specialist 2
- Posts: 264
- Joined: Wed Nov 18, 2009 6:18 am
- Location: Western Australia
Great thread , very helpful.Your air bottle looks very good and durable, Good Job
. Just a Few quick questions.
what type of bottle did you use ? like brand ( the one with the concave bottom) other two bottles look like Pepsi bottles.
how did you round out the bottom of the bottle ? i know, heat obviously but tell details
related to previous question - how did you heat shrink the larger bottles ?and evenly

what type of bottle did you use ? like brand ( the one with the concave bottom) other two bottles look like Pepsi bottles.
how did you round out the bottom of the bottle ? i know, heat obviously but tell details
related to previous question - how did you heat shrink the larger bottles ?and evenly
That bottle would have held 80 psi just fine without any reinforcing. 150 psi though... may be good you reinforced it.
The actual brand I used was Glaceau, Smart Water. I really like these bottle because they haven't switched to the annoying smaller bottle caps, and they have straight sides and thicker plastic than most water bottles now. The larger bottles I shrank around the outside were Lipton Citrus Green Tea 1.5L bottles.Major Collins wrote:Great thread , very helpful.Your air bottle looks very good and durable, Good Job. Just a Few quick questions.
what type of bottle did you use ? like brand ( the one with the concave bottom) other two bottles look like Pepsi bottles.
how did you round out the bottom of the bottle ? i know, heat obviously but tell details
related to previous question - how did you heat shrink the larger bottles ?and evenly
Rounding out the bottom is actually something used in water rocketry, called "guppying". Basically you pressurize the bottle slightly (I use 20 PSI) then heat up the area you want to expand. To pressurize the bottle you can put a tire valve into a bottle cap with a small hole in it. If the stem of the valve is long enough you can put it into a drill and use that to rotate the bottle while you're heating it.
To shrink down the outer bottles, you have to fill the innermost bottle with water. This keeps it cool and prevents it from shrinking. With the outer bottle on, hold the heat gun at one end (I start on the end which need the most shrinking) of the bottle and rotate the bottle on a table or something similar. Slowly work your way along the bottle until the entire sleeve is shrunk.
As long as you keep the bottle moving, everything will shrink evenly. It just takes a bit of practice, and since I use this technique for making water rocket shells, I've gotten good at it.
- - - - - - - - - -
I'm actually working on a second tank now, a larger 1.5L one, with 2L bottles for exterior sleeves. I could try it with a 2L bottle, but I only have 1 bottle (2.25L or something) that would fit outside, so I can't do it.
I should be able to do a 150 PSI pressure test and impact test on my first 1L tank, and I'll try to get video of that.
- Technician1002
- Captain
- Posts: 5189
- Joined: Sat Apr 04, 2009 11:10 am
If you monitor the pressure and bleed it off when it becomes excessive, a source for high pressure is dry ice and water. I have used this in the past to do some pressure testing.
Do not ignore the test and become distracted while waiting for the pressure to build. Don't take a bathroom break and check it later.. Monitor it full time while testing.
Do not ignore the test and become distracted while waiting for the pressure to build. Don't take a bathroom break and check it later.. Monitor it full time while testing.
As I'm only 16 I'm not allowed to purchase dry ice, so this isn't possible for me. My compressor has a max of 150 PSI, so that's all I'll ever be using anyways.Technician1002 wrote:If you monitor the pressure and bleed it off when it becomes excessive, a source for high pressure is dry ice and water. I have used this in the past to do some pressure testing.
Do not ignore the test and become distracted while waiting for the pressure to build. Don't take a bathroom break and check it later.. Monitor it full time while testing.
Just wondering though, what's the maximum pressure dry ice can produce?
- - - - - - - - - -
Here is the test video I just shot:
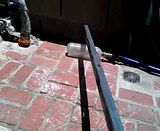
The bottle was filled with water, pressurized to 135 PSI, then hit 11 times with a large metal level. The hits get progressively harder, and you can see how much the tank itself bounces (while filled with water). I was afraid it might blow up in my face so I didn't hit it very hard, but it's more abuse than tanks normally go through.
To connect the air hose I modified a 1/4" quick connect adapter and added a rubber washer and stuck it into a bottle cap. It sealed better at higher pressures. I'm tempted to see if I can cast an adapter into a fitting of some sort with epoxy.