hybrid cartridge protoype without burst disk
- jackssmirkingrevenge
- Five Star General
- Posts: 26216
- Joined: Thu Mar 15, 2007 11:28 pm
- Has thanked: 576 times
- Been thanked: 347 times
I was intending to make an experimental hybrid cartridge as discussed here but hit upon a snag. My initial thoughts were to have an ignitor contact on the cartridge body and one on the filling schrader, with the spark gap in between, but with a 3/8" body I'm worried that the spark will jump through the epoxy instead of through the air. I would prefer to use a standard schrader than come up with my own filling valve for ease of manufacture.
The design is illustrated below, are my fears justified?
The design is illustrated below, are my fears justified?
- Attachments
-
- hybridsealcart.JPG (22.54 KiB) Viewed 12424 times
Last edited by jackssmirkingrevenge on Thu Oct 22, 2009 4:39 pm, edited 1 time in total.
hectmarr wrote:You have to make many weapons, because this field is long and short life
I'm not sure. Are there any out of the ordinary ingredients in the epoxy?
My initial guess would say air is still the path of least resistance. In my experience with sparking, I've never had issues with the spark going somewhere else other than the intended gap (even in small bore). The bigger problem was it sparking outside of the chamber, especially under pressure.
You may want to consider insulating the exposed rear of the schrader somehow so the spark doesn't jump on the outside of the cartridge? Unless you've already thought of that
My initial guess would say air is still the path of least resistance. In my experience with sparking, I've never had issues with the spark going somewhere else other than the intended gap (even in small bore). The bigger problem was it sparking outside of the chamber, especially under pressure.
You may want to consider insulating the exposed rear of the schrader somehow so the spark doesn't jump on the outside of the cartridge? Unless you've already thought of that
- rcman50166
- Corporal 2
- Posts: 697
- Joined: Sat Jan 19, 2008 7:11 pm
- Location: Bethel, CT
- Contact:
Epoxy Resin has a dielectric constant of 3.6. In comparison PVC has a constant of 1.4 and glass has a constant of 4.8. Turns out you should be more worried about arcing to PVC pipe than to epoxy

- jackssmirkingrevenge
- Five Star General
- Posts: 26216
- Joined: Thu Mar 15, 2007 11:28 pm
- Has thanked: 576 times
- Been thanked: 347 times
Wouldn't it still be more likely to arc through the epoxy than the air though?
To be safe, I see two options:
1) move on to a wider tube, not keen on this as I would really like to use this particular brass tubing as it's about the same diameter as a 9mm cartridge case
2) discard the schrader and make my own non-return valve, that can be simply a nail with an o-ring slipped on passing through an appropriately sized tube. It could be held with a springy bit of wire that would also serve as a spark contact, as shown below. Pressurising would be done by creating another chamber into which the cartridge would fit for pressurising after the fuel is injected and BB put in place. Bit of a headache though, if it is to be done on a regular basis...
To be safe, I see two options:
1) move on to a wider tube, not keen on this as I would really like to use this particular brass tubing as it's about the same diameter as a 9mm cartridge case

2) discard the schrader and make my own non-return valve, that can be simply a nail with an o-ring slipped on passing through an appropriately sized tube. It could be held with a springy bit of wire that would also serve as a spark contact, as shown below. Pressurising would be done by creating another chamber into which the cartridge would fit for pressurising after the fuel is injected and BB put in place. Bit of a headache though, if it is to be done on a regular basis...
- Attachments
-
- hybridsealcart2.JPG (15.51 KiB) Viewed 12383 times
hectmarr wrote:You have to make many weapons, because this field is long and short life
- Technician1002
- Captain
- Posts: 5189
- Joined: Sat Apr 04, 2009 11:10 am
Dielectric constant is related to how much capacitance a material provides in relation to air. For example 2 metal plates separated by air will change in capacitance if the air is replaced by glass PVC or epoxy. Glass will increase the value by 4.8 for example. The voltage where an arc will punch a hole in it is Dielectric strength. You were so close to the right answer. Go try again.rcman50166 wrote:Epoxy Resin has a dielectric constant of 3.6. In comparison PVC has a constant of 1.4 and glass has a constant of 4.8. Turns out you should be more worried about arcing to PVC pipe than to epoxy
Air has a dielectric constant of 1.0.
Now compare the dielectric strengths.

Start here;
Scroll down the table to the line of dielectric strengths. This table give them in Volts/mil. There are several varieties of PVC. The one in the table is as high a HDPE a well known high voltage insulator.
For someone who builds Tesla coils, I figured you knew about voltage breakdown and differences in air capacitors and glass plate capacitors.
A plate glass tuning cap on a Tesla coil primary only need to be about 1/5th the area of an air gap capacitor with the same plate spacing.
In a Tesla coil you need to be concerned with building a tuning cap of both the correct value as well as the correct breakdown voltage.
Last edited by Technician1002 on Wed Oct 21, 2009 2:58 pm, edited 1 time in total.
- Willdebeers
- Specialist 2
- Posts: 214
- Joined: Tue Feb 03, 2009 1:18 pm
I doubt it would arc, but to be sure, why dont you put a rubber sleeve around the schrader valve, stopping the arc? 

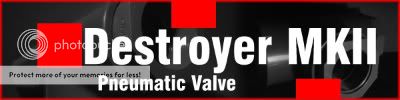
- Moonbogg
- Staff Sergeant 3
- Posts: 1736
- Joined: Mon Oct 13, 2008 10:20 pm
- Location: SoCal
- Has thanked: 165 times
- Been thanked: 102 times
That may provide a loose hold on the schrader. It would wiggle around a bit and may even blow out without direct adhesion.Willdebeers wrote:I doubt it would arc, but to be sure, why dont you put a rubber sleeve around the schrader valve, stopping the arc?
EDIT: You may consider using a strong plastic plug in place of the epoxy and then epoxy the plug in place and thread it and then screw and epoxy the schrader in that.
- POLAND_SPUD
- Captain
- Posts: 5402
- Joined: Sat Oct 13, 2007 4:43 pm
- Been thanked: 1 time
AFAIK resins are often used for insulating electrical equipment
Children are the future
unless we stop them now
unless we stop them now
- jackssmirkingrevenge
- Five Star General
- Posts: 26216
- Joined: Thu Mar 15, 2007 11:28 pm
- Has thanked: 576 times
- Been thanked: 347 times
What the heck, I'll give it a go. Tomorrow though, it's past the time when workshop noises are socially acceptable in an urban setting 
If it doesn't work I'll go with the larger diameter tubing.

If it doesn't work I'll go with the larger diameter tubing.
hectmarr wrote:You have to make many weapons, because this field is long and short life
- rcman50166
- Corporal 2
- Posts: 697
- Joined: Sat Jan 19, 2008 7:11 pm
- Location: Bethel, CT
- Contact:
The dielectric constant is based on conductivity of air. Dielectric Constant of Air = 1jackssmirkingrevenge wrote:Wouldn't it still be more likely to arc through the epoxy than the air though?
To be safe, I see two options:
1) move on to a wider tube, not keen on this as I would really like to use this particular brass tubing as it's about the same diameter as a 9mm cartridge case![]()
2) discard the schrader and make my own non-return valve, that can be simply a nail with an o-ring slipped on passing through an appropriately sized tube. It could be held with a springy bit of wire that would also serve as a spark contact, as shown below. Pressurising would be done by creating another chamber into which the cartridge would fit for pressurising after the fuel is injected and BB put in place. Bit of a headache though, if it is to be done on a regular basis...

Could work, but then also put epoxy between the shrader and the rubber.Willdebeers wrote:I doubt it would arc, but to be sure, why dont you put a rubber sleeve around the schrader valve, stopping the arc?
- rcman50166
- Corporal 2
- Posts: 697
- Joined: Sat Jan 19, 2008 7:11 pm
- Location: Bethel, CT
- Contact:
Well isn't the dielectric constant directly proportional to the voltage rating of the material? I remember building my primary capacitor using a calculation that did not include the dielectric rating, merely involving the area and spacing. Based on this it was shown that decreasing distance between plates increased capacitance. The dielectric material was assumed to be present as a simple insulator to make it capable to bring the plates closer together than an open air capacitor. Thus, it made sense that the dielectric constant was proportional to voltage ratingTechnician1002 wrote:Dielectric constant is related to how much capacitance a material provides in relation to air. For example 2 metal plates separated by air will change in capacitance if the air is replaced by glass PVC or epoxy. Glass will increase the value by 4.8 for example. The voltage where an arc will punch a hole in it is Dielectric strength. You were so close to the right answer. Go try again.rcman50166 wrote:Epoxy Resin has a dielectric constant of 3.6. In comparison PVC has a constant of 1.4 and glass has a constant of 4.8. Turns out you should be more worried about arcing to PVC pipe than to epoxy
Air has a dielectric constant of 1.0.
Now compare the dielectric strengths.
Start here;
Scroll down the table to the line of dielectric strengths. This table give them in Volts/mil. There are several varieties of PVC. The one in the table is as high a HDPE a well known high voltage insulator.
For someone who builds Tesla coils, I figured you knew about voltage breakdown and differences in air capacitors and glass plate capacitors.
A plate glass tuning cap on a Tesla coil primary only need to be about 1/5th the area of an air gap capacitor with the same plate spacing.
In a Tesla coil you need to be concerned with building a tuning cap of both the correct value as well as the correct breakdown voltage.

- Technician1002
- Captain
- Posts: 5189
- Joined: Sat Apr 04, 2009 11:10 am
My oops, I referred to a table of plastics and then didn't post the link. Plastics commonly used in high voltage applications are listed in this.rcman50166 wrote:
Well isn't the dielectric constant directly proportional to the voltage rating of the material? I remember building my primary capacitor using a calculation that did not include the dielectric rating, merely involving the area and spacing. Based on this it was shown that decreasing distance between plates increased capacitance. The dielectric material was assumed to be present as a simple insulator to make it capable to bring the plates closer together than an open air capacitor. Thus, it made sense that the dielectric constant was proportional to voltage rating
http://www.machinist-materials.com/comp ... astics.htm
Note that Delrin Acetel compared to Polysulfone is opposite. The higher dielectric constant material has the lower dielectric strength.
Material Strength Constant
Delrin 380 3.7
Poly 425 3.15
Some materials vary the value of the dielectric constant over frequency.
In many high voltage applications it is desirable to insulate components but not have the insulation add to the capacitance. This is where low capacitance high voltage high frequency low capacitance coax cable get their design.
Withstanding high voltage is important. Having low capacitance is important. Low capacitance speaker cable to prevent shunting high frequencies is commonly seen in audiophile equipment.
Edit, This is why Poly capacitors are common in electronics. It's high dielectric constant makes high value capacitors in smaller spaces.
- jackssmirkingrevenge
- Five Star General
- Posts: 26216
- Joined: Thu Mar 15, 2007 11:28 pm
- Has thanked: 576 times
- Been thanked: 347 times
Construction in progress, figured I'd improve my chances by slimming down the schrader a little 
edit: cartridge is curing, I canted the schrader slightly as Copperboy suggested above. We'll see how it works tomorrow.

edit: cartridge is curing, I canted the schrader slightly as Copperboy suggested above. We'll see how it works tomorrow.
- Attachments
-
- the bits before epoxy treatment. It took me a remarkably small amount of time to put this together, if it works they should be easy to manufacture in quantity.
- DSCF4405.JPG (18.43 KiB) Viewed 12258 times
hectmarr wrote:You have to make many weapons, because this field is long and short life